Overview
Raw material processing
Mr. Fukunishi produces Uda paper from kozo, which he himself cultivates in Yoshino, but also from kozo that is grown in Ibaraki Prefecture and Kochi Prefecture. The branches of the kozo tree are cut to the same lengths and boiled, the outer black bark (kurokawa) and inner green bark (amakawa) are removed, and the branch is further scraped away until only the inner white part (shiroso) remains.
The shiroso is then washed in the waters of Yoshino River, which flows in front of Mr. Fukunishi’s home, and sun-dried. After removing any impurities from the shiroso in the chirikiri process, the shiroso is cooked with wood ash and then washed in water, and cleared of any remaining impurities by hand.
Then, the shiroso is beaten by hand in a process called kamisouchi. This kamisouchi, done manually, is what gives Uda paper its high quality.
Preparation for paper formation
The neri from the noriutsugi (panicle hydrangea plant) grown in Hokkaido is prepared two days in advance by beating the plant, then immersing it in water, and filtering with a fabric to extract the viscous liquid.
White clay is added to give Uda paper its characteristic quality. White clay helps make supple yet strong and smooth paper. Water drawn from the Yoshino Mountain, the beaten kozo, and the grinded white clay are placed in a large vat and thoroughly mixed using a large comb-like tool called zaburi to make the paper stock.
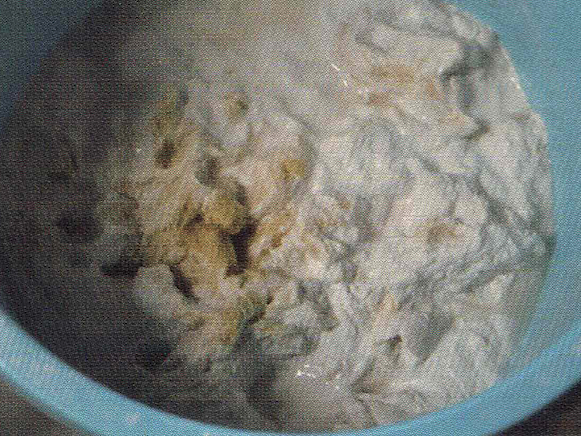
Stock mixed with white clay
The neri is then added to the stock in preparation for papermaking.
Paper formation and drying
Neri works well in cold weather, as in making Misu paper, so papermaking is done mainly from around September to April. Uda paper is made in various sizes, but a wide screen measuring 32cm high and 145cm long (approx. 21 screen lines per traditional measuring unit of sun (3cm)) is generally used.
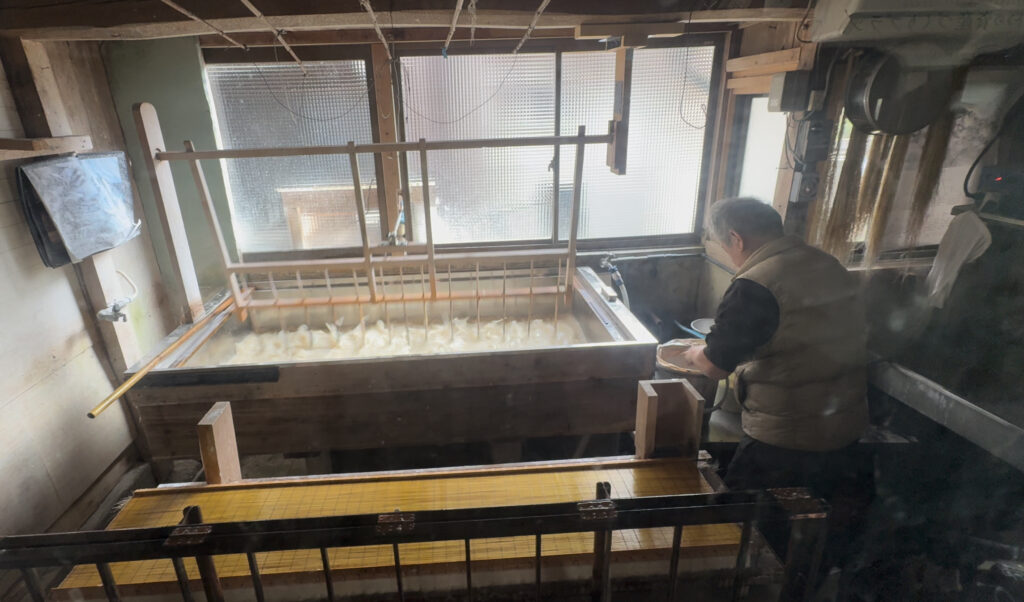
Paper formation
The paper stock is scooped a number of times, and the mould is shaken in the vertical direction before letting the flow of the stock settle gradually. The paper that has formed is placed on a board called shito one sheet at a time and drained of water.
After further dewatering the paper by applying pressure to the pile, each sheet is taken from the pile, pasted on a pine board that is about 230cm long and 35cm wide, and sun-dried.
Kamisouchi
The traditional hand-beating process called kamisouchi has been firmly kept in the making of Misu paper and Uda paper. After the fibers are cooked with wood ash and washed, they become considerably soft.
These fibers are then beaten first using a machine, then placed on a stone board and beaten evenly and rhythmically with oak beating sticks held in both hands, to further loosen the fibers. Fibers worth 200 sheets of Misu paper are beaten for approximately an hour, and fibers worth 100 sheets of Uda paper are beaten for some two hours.
The time and effort that goes into this manual task separate the fibers even more thoroughly and makes for an even more supple paper.

Kamisouchi
White clay
It may come as a surprise to hear that some papers contain clay.
Although they make up only a small portion of all papers, other papers containing clay, besides Uda paper such as maniaigami, have traditionally been made, besides Uda paper. The white clay that is used to make Uda paper comes from rocks quarried from Yoshino Mountain.
Today, rocks crushed using a hammer are placed in a drum machine with water and spun for about 40 hours, to reduce them to fine grains in a white-colored liquid. The supernatant water is scooped up and dried over an extended period of time.
When using this dried white clay as a stock ingredient, it is mixed with water and filtered through a cotton fabric.
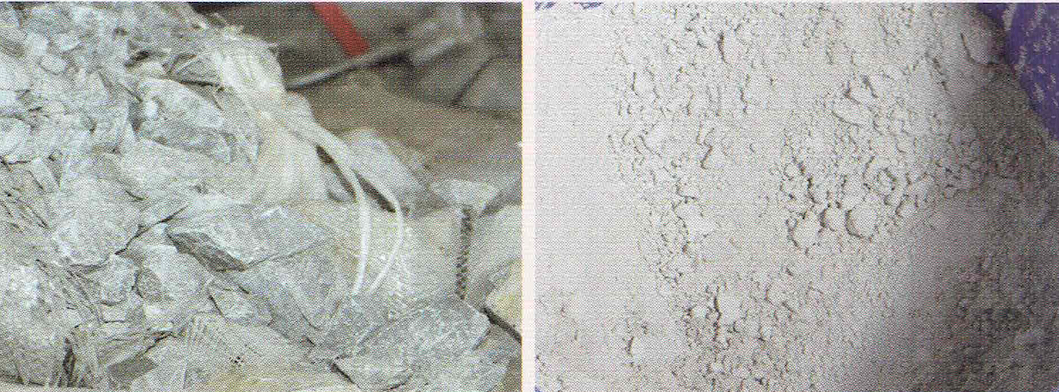
More detailed explanation
From a brochure published by Fukunishi Washi Honpo.
( 1 ) Harvesting of Kozo tree.
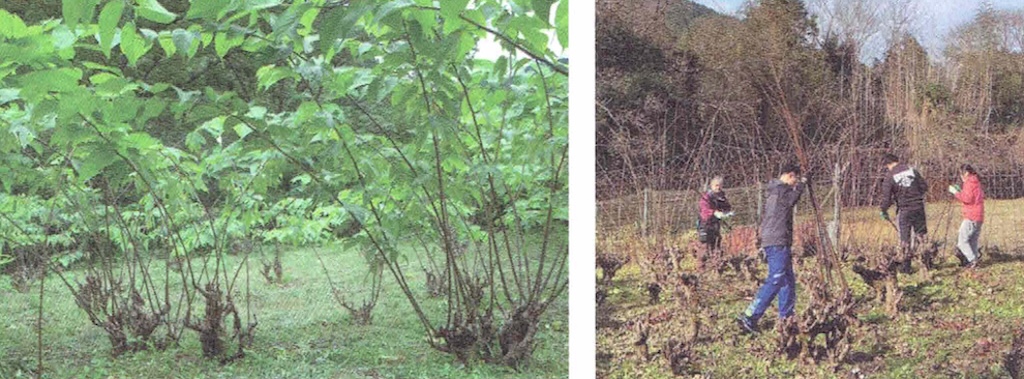
( 2 ) Steam Kozo for about four hours.
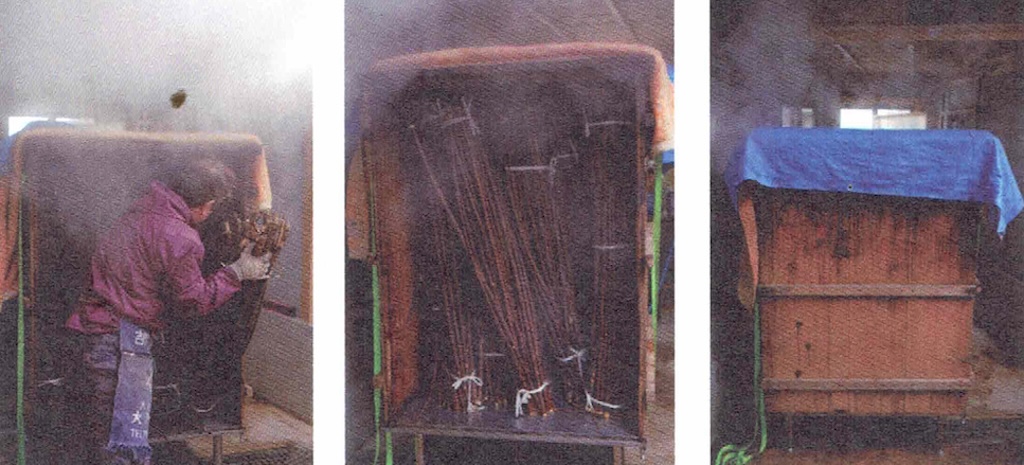
( 3 ) Peel the bark from branches while they are hot. This bark is called “Kuroso ( Black Kozo) “.
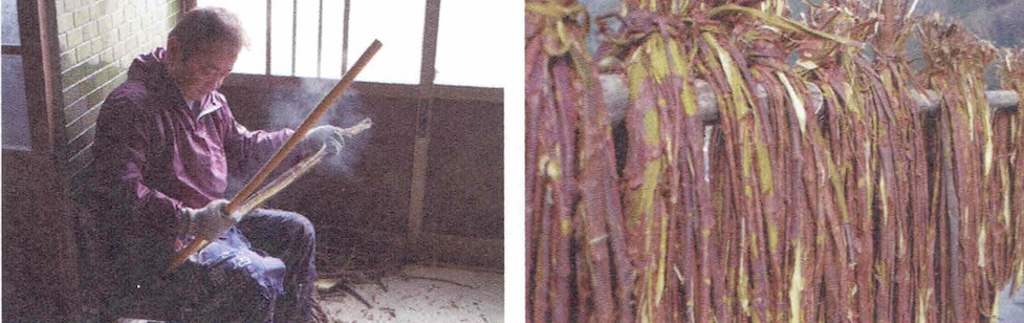
( 4 ) Remove the bark from the Kozo sticks. This is called Shiroso ( White Kozo ) .
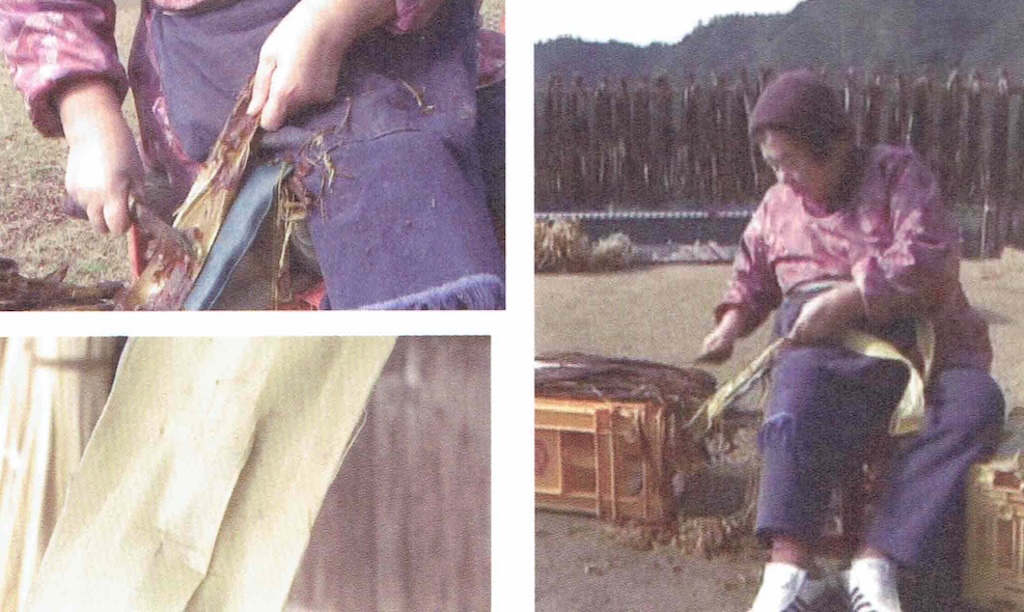
( 5 ) Soak the Shiroso in the river water and then dry it.
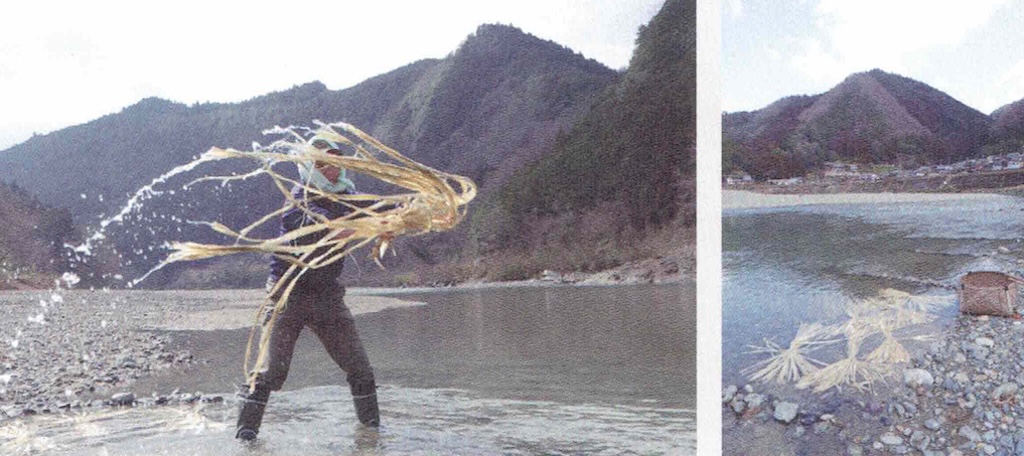
( 6 ) To make the fibers of “Shiroso” tighter, it is dried in the sun.
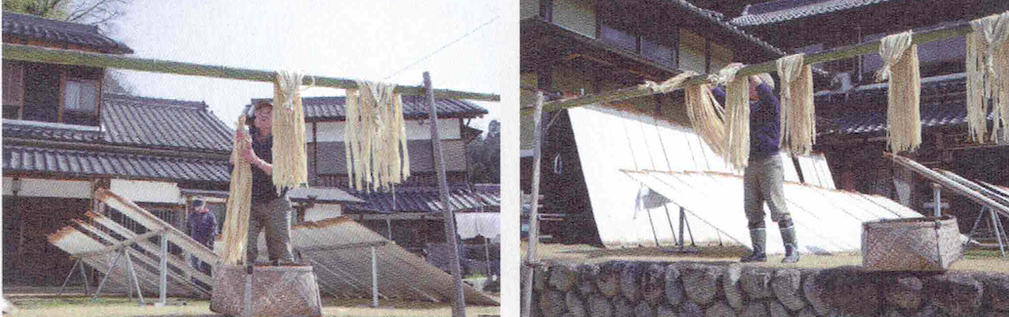
( 7 ) Remove the holes in the Shiroso.
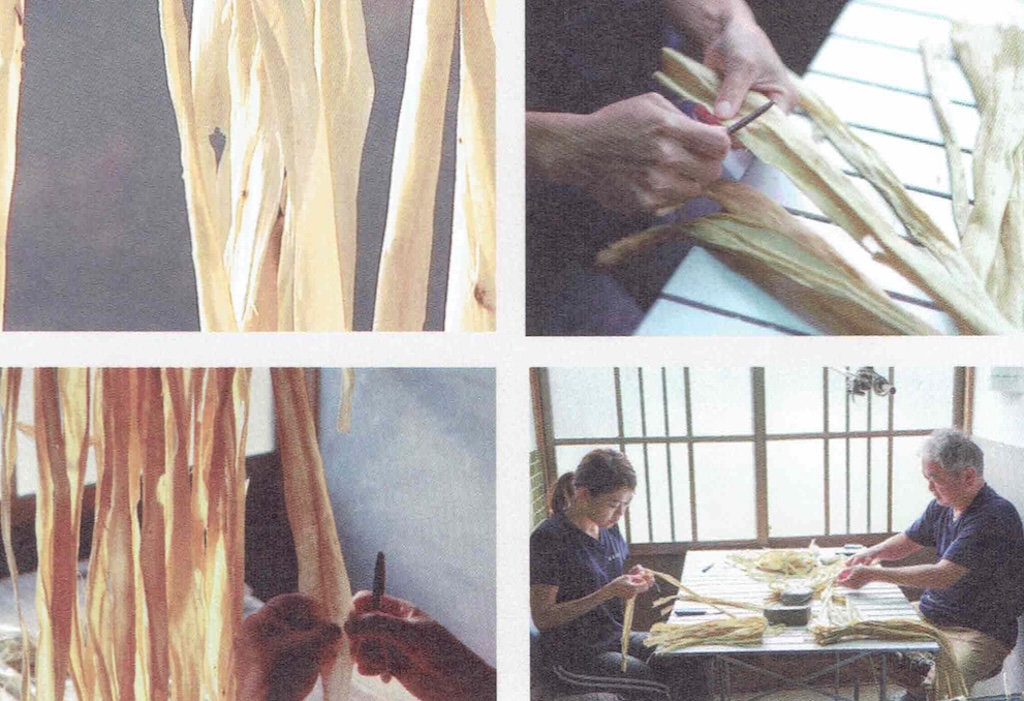
( 8 ) Boil the Shiroso in lye
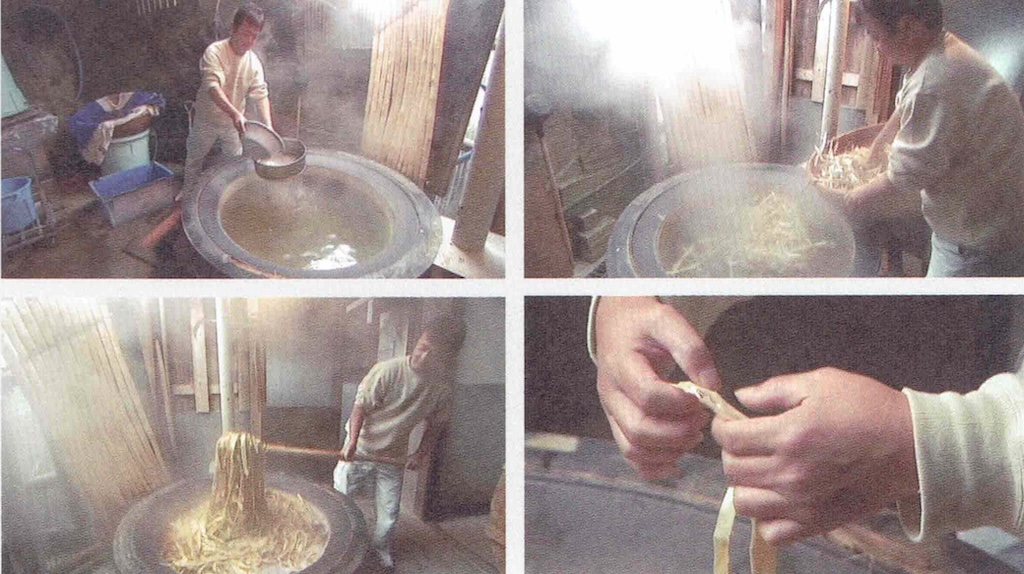
( 9 ) Rinse the Kamiso ( “raw paper” previously called Shiroso. ) in water to wash away the lye.
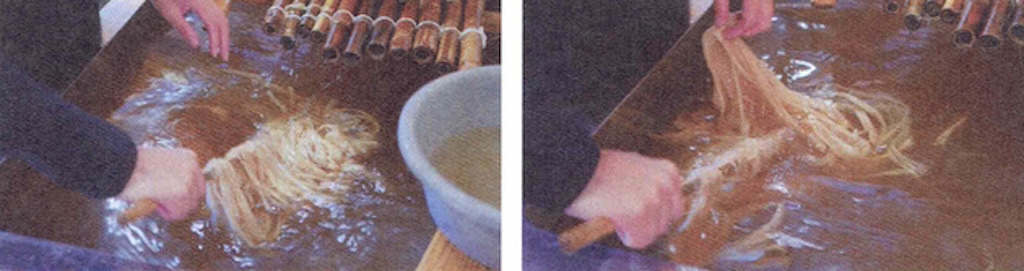
( 10 ) Carefully remove the dust from the Kamiso.
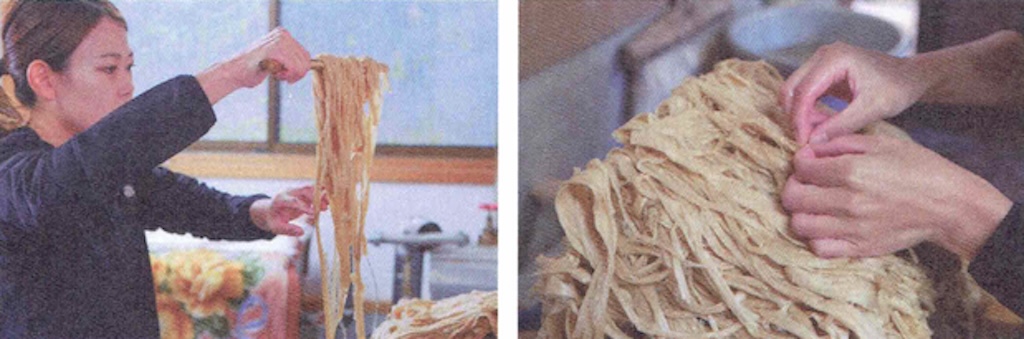
( 11 ) Carefully pound Kamiso on a stone with an oak stick.
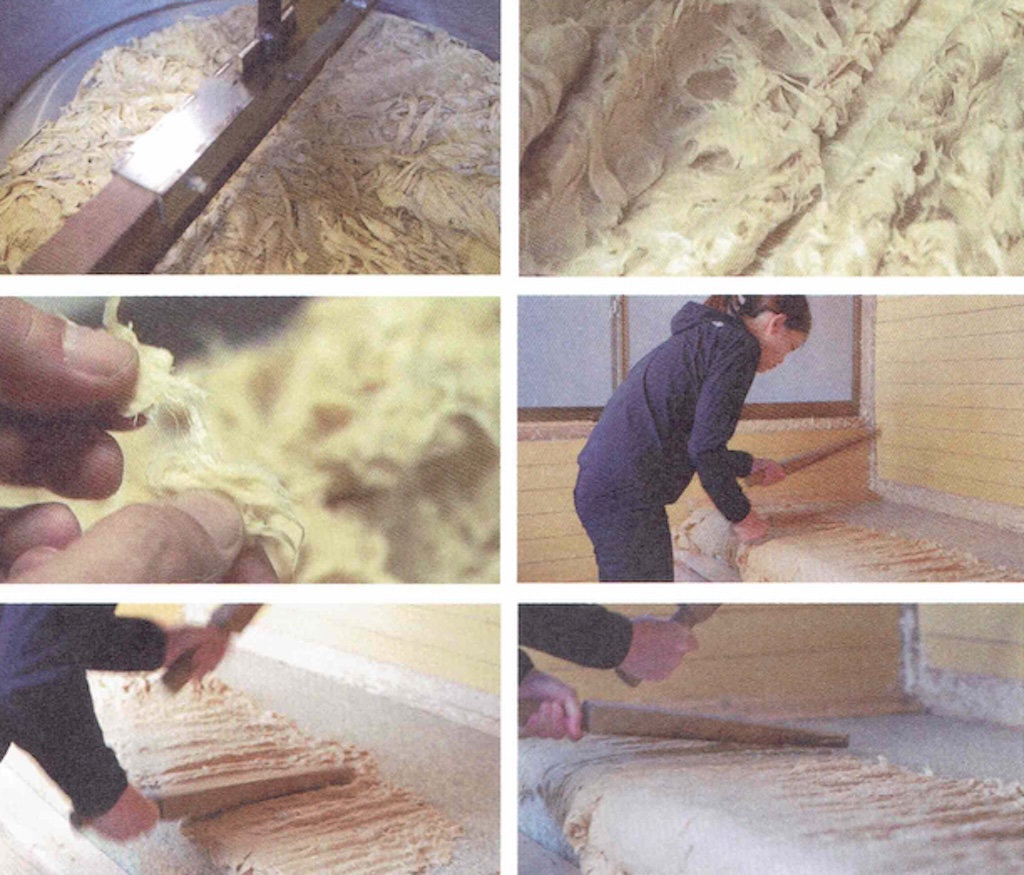
( 12 ) Mix finely scraped Panicle Hydranger bark with white clay.
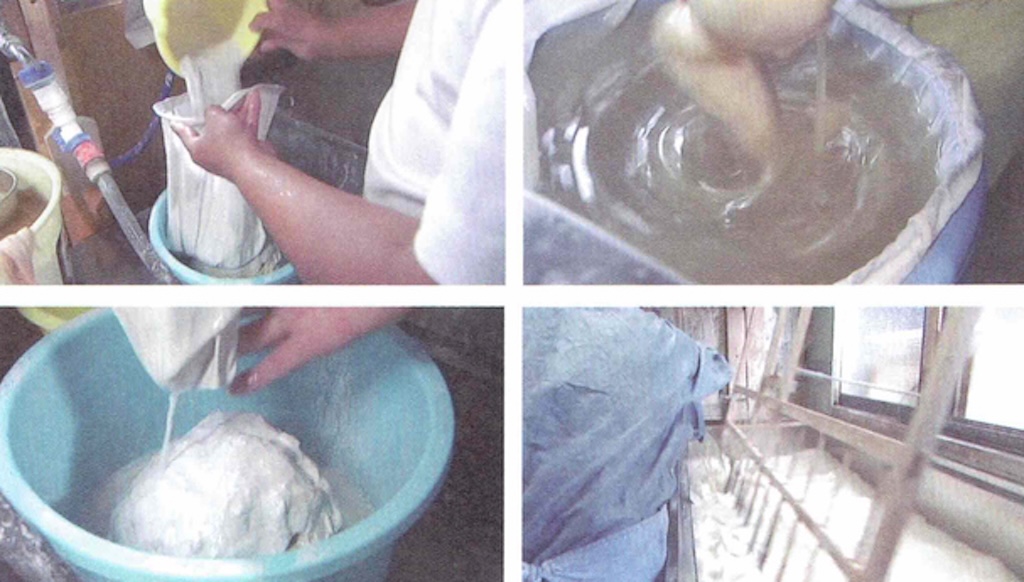
( 13 ) Mold the paper
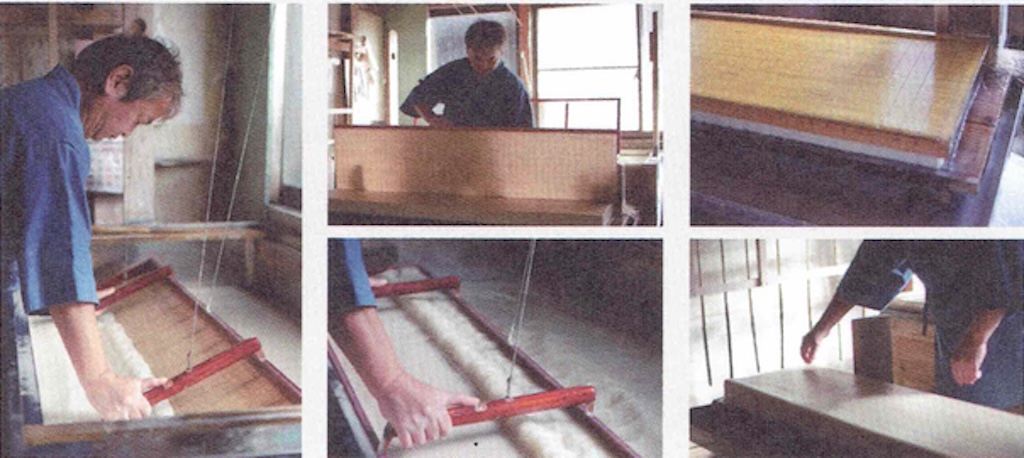
( 14 ) Place a weight on the paper to push out the water.
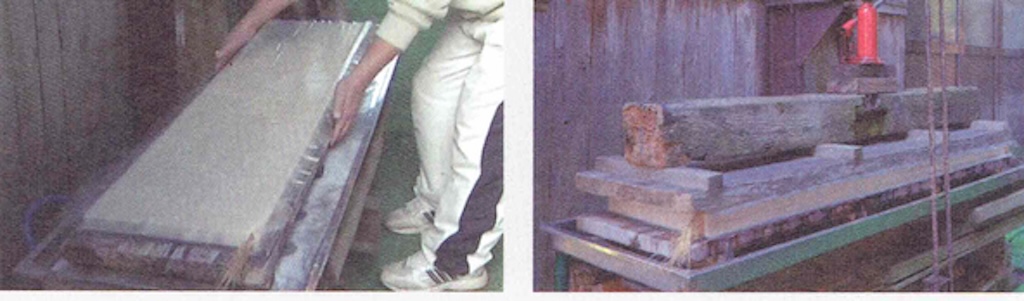
( 15 ) The paper is pasted onto the pine board with a horsehair brush and dried in the sun.
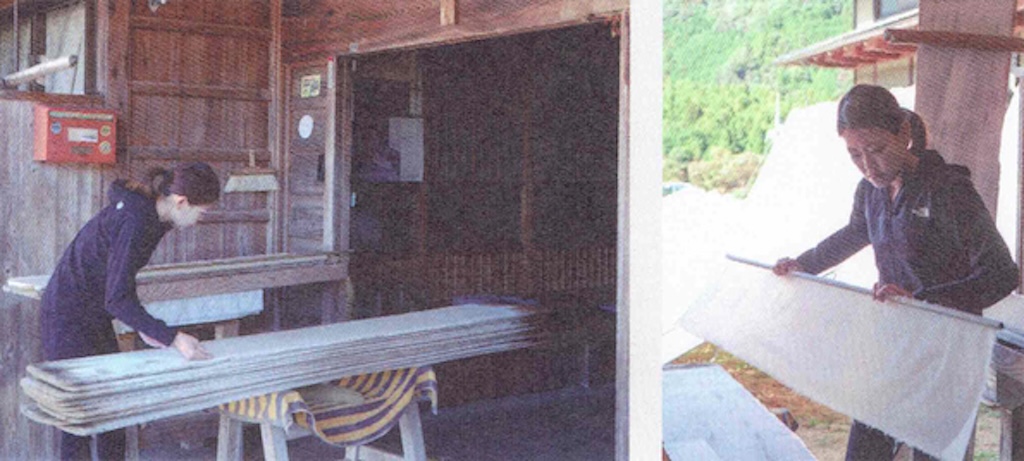
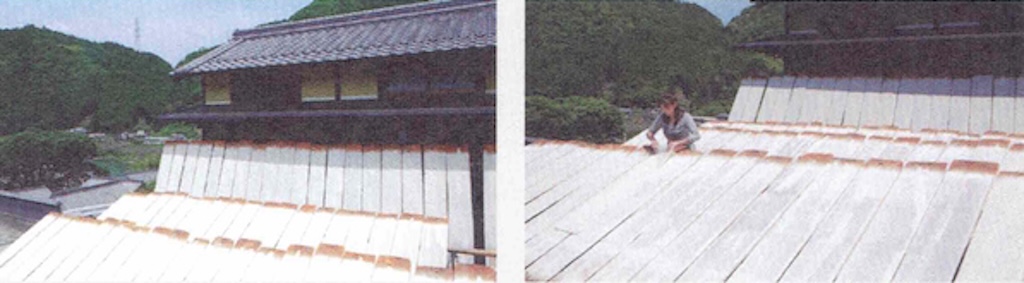
( 16 ) Sort the paper and prepare it for shipping.
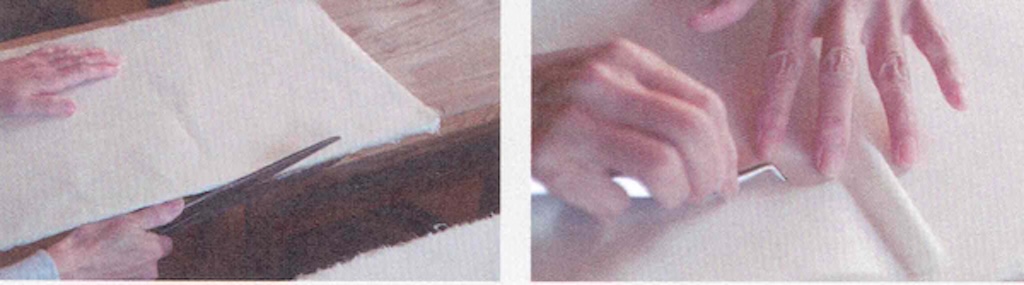
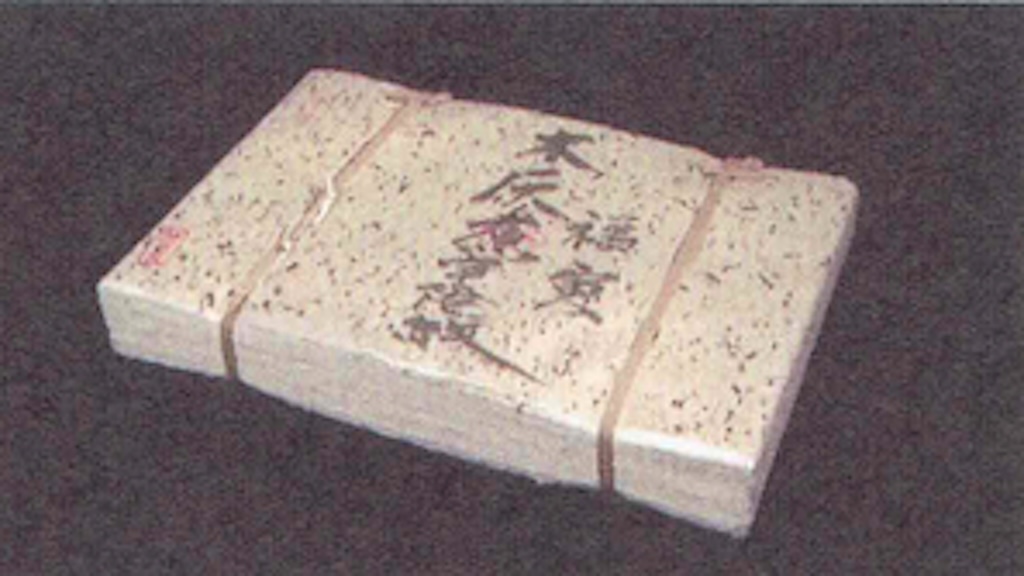